Droplet separators
Vane type separators
Vane type separators typically consist of parallel profiles that determine the efficiency of the separator based on their shape and length in the flow direction. A more curved and complex profile allows for the separation of smaller droplets, as their mass inertia causes them to be separated from a straighter and simpler profile. When a finer droplet spectrum is required for separating liquid droplets from gas streams, vane type separators are commonly used for both vertical and horizontal gas streams. When there is a risk of dirt deposition the separators can be flushed discontinuously or continuously. In extreme cases, a multistage system may be necessary, with the first separation phase being rinsed particularly intensively. Vane type separators achieve a high separation rate of 99.9%. The main difference between vertically and horizontally flown vane type separators lie in the construction, the vanes of a vertical type are tilted horizontally or at a small angle to the horizontal plane, and the liquid must flow down in the opposite direction of the gas. The design of a vertically inflowed separator profile should include low-speed zones on the profiles, where deposited liquid droplets can accumulate without interacting with the gas flow above them. These zones are also utilized for effectively removing the liquid droplets from the lamella separator. A gas flow loaded with droplets is passes a labyrinth consisting of curved and profiled vanes. The liquid droplets, which enter the gas stream, are diverted from their original path due to mass inertia, within this labyrinth. The efficiency of this separation process depends on factors such as the geometry of the profiles, the properties of the gas and the liquid, the droplet size, and the droplet load. If a droplet comes into contact with the profile wall of the vanes, it is considered a boundary droplet and is completely separated under specific conditions. Droplets with a diameter equal to or larger than this boundary droplets are also completely separated. However, droplets smaller than the boundary droplets are only partially separated, resulting in a fractional separation rate. This rate can be used to evaluate the performance of the separation system. This part can be considered as a fractional separation rate.
Wire mesh demisters
The principle behind the operation of a wire mesh demister, similar to a vane type separator, relies on mass inertia. When the size of the liquid droplets to be separated is considerably smaller than 10 microns, a wire mesh demister can be used. This demister is constructed using thin threads that are intricately woven into a three-dimensional mat. The demister mat can be customized into various shapes, allowing its application in vertically flowing systems. For applications where the diameter is smaller, a single-part separator is often utilized, while larger surfaces require multiple parts to facilitate removal through a manhole. The efficiency of the demister is determined by the composition of the mat, with a thin wire arrangement that minimizes the gap between wires being ideal for separating fine droplets. Cleaning a wire mesh demister is challenging, making it suitable only for liquids that do not result in dirt deposition. Consequently, the use of a wire mesh demister is often not feasible in dirty applications. It is quite common to achieve separation grades of 99.9% for droplet sizes ranging from 5 to 20 microns using a wire mesh demister. However, unlike vane type separators for vertical flow, there are significant pressure losses to consider, ranging from 1.5 to 4 mbar. These losses depend heavily on the liquid load of the gas. It is important to note that wire mesh demisters can only be used as fine separators due to the risk of dirt deposition and package clogging. During the separation process, the droplets pass through the filter mat, collide with the wire surface due to mass inertia, and agglomerate at the wires before falling back as larger droplets. The separation performance is influenced by the free volume and specific wire surface of the mat, and it improves with increasing gas rate. However, it is crucial not to exceed the maximum velocity to avoid flooding, which refers to the dragging of drops. For a 99.9% fractional separation rate, the limit droplet size typically falls within the range of 5 to 10 microns for standard versions. However, with special constructions and appropriate design, it is possible to achieve such separation for droplets as small as 3 microns. To support the demister mats, specially designed support and/or cover grids are usually supplied, which are designed in such a way that the free flow surface is about 90%. When installing the wire mesh demister, care must be taken to ensure that the demister mat fits snugly to the column wall so that false air cannot escape. The mat height of the wire mesh demister is 100 to 150 mm for most applications. If the gas flow contains very fine droplets, such as those caused by condensation, a significantly larger mat height or a multi-layer structure may be required.
Open spray systems
This type of scrubber operates using a closed loop pump system, where the washing liquid is pumped from the integrated buffer. To ensure an extended spraying process, the scrubber system is equipped with multiple fully removable spray lances arranged in layers. These spray lances consist of spray nozzles, some of which are mounted co-current and others are counter current. The precise positioning of these spray nozzles within the scrubber is crucial for effective gas treatment, as it allows for thorough contact between the washing fluid and the process gas, thereby capturing particles. The tangential nozzles, which are designed to prevent clogging, produce fine droplets with a uniform spray pattern to maximize the capture of dust and gas particles. By ensuring optimal absorption, a significant reduction in pollutant particles and gases can be achieved. The design of the scrubber system ensures that the spray nozzles, with their high combined flow rate, simultaneously clean the interior of the washing section. The overlapping spray pattern created by the positioning of the spray nozzles results in an extremely efficient cleaning system. This means that the contaminated gases cannot pass through the spray section without being absorbed. Consequently, the need for a packing, which would increase pressure loss, is eliminated, resulting in an exceptionally low and consistent pressure loss. This type of scrubber is particularly suitable for handling irregular concentrations or peak discharges, while the liquid to gas ratio is not that sensitive as in packed bed scrubbers.

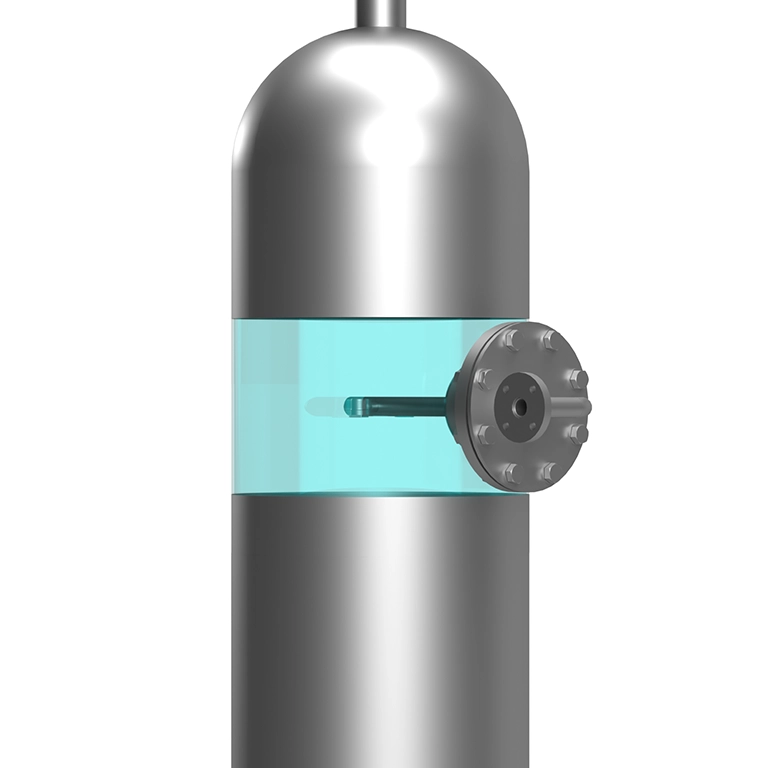
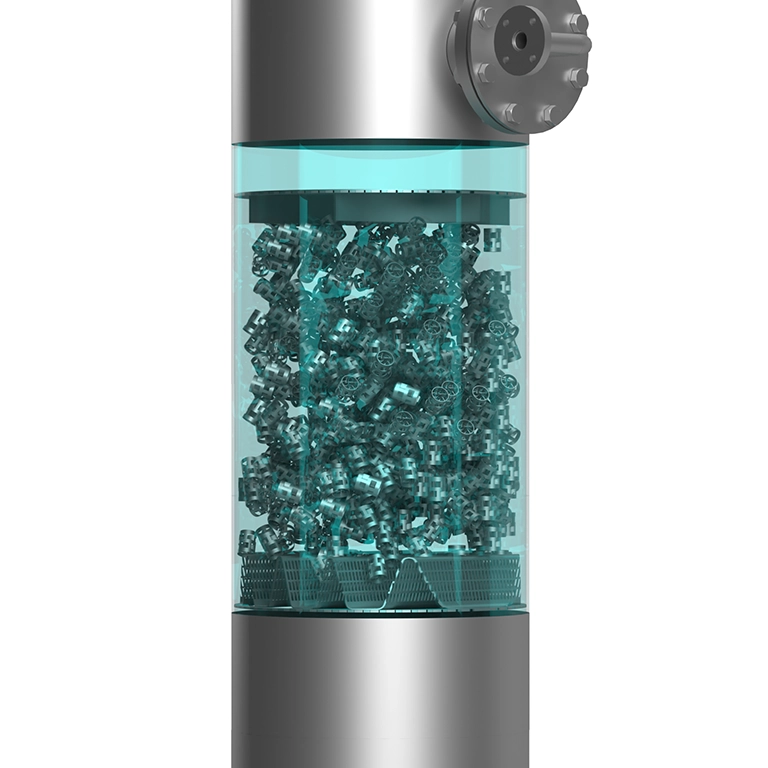
Hollow cone nozzles
This type of spray nozzle is quite popular because of a very important property: droplet size. Hollow cones produce finer droplets than any other types of hydraulic (single phase) nozzles. The biggest advantage of fine droplets is that the surface area of all accumulated droplets is enormous in relation to the other types mentioned. There are two types of hollow cone nozzles; axial and tangential inlet. The incoming fluid flow in axial nozzles is in line with the connection where the fluid in the nozzle is set into rotation by a specific swirl body. This rotating liquid stream is then sprayed into the environment through a nozzle opening, creating the shape of a hollow cone. Tangential hollow cone nozzles are much simpler in construction than axial nozzles. A tangential incoming liquid flow sets it into rotation, providing the cylindrical inside of the nozzle with a liquid film that influences the size of the drop. When the liquid film is discharged out of the nozzle via the spray opening, a cone-shaped spray pattern is created. Eccentric hollow cone nozzles are much less susceptible to clogging than axial types due to their lateral entry and therefore the lack of a vertebral body. The hollow cone nozzles are mainly used by Ravebo in gas scrubbers and quenchers because of their homogeneous spray pattern with fine droplets.
Full cone nozzles
Full cone nozzles are used for a wide variety of applications. These spray nozzles also have a cone-shaped spray pattern, but here the cone is closed. This means that the full cone nozzle is the first choice when an even surface flooding or liquid distribution is required. In contrast to hollow cone nozzles, full cone nozzles produce a fairly coarse droplet that has a greater kinetic energy compared to hollow cone nozzles. This means that the impact on the spraying surface is much higher. Because of these properties, this type of spray nozzle is often used for cleaning applications. Just like hollow cone nozzles, full cone nozzles are designed as axial and tangential nozzles. Both types have a swirl body that influences the rotating flow. Without these elements the nozzle would give a kind of hollow cone appearance. Full cone nozzles are mainly used by in scrubbers with a packed bed because of their good liquid distribution and distribution.
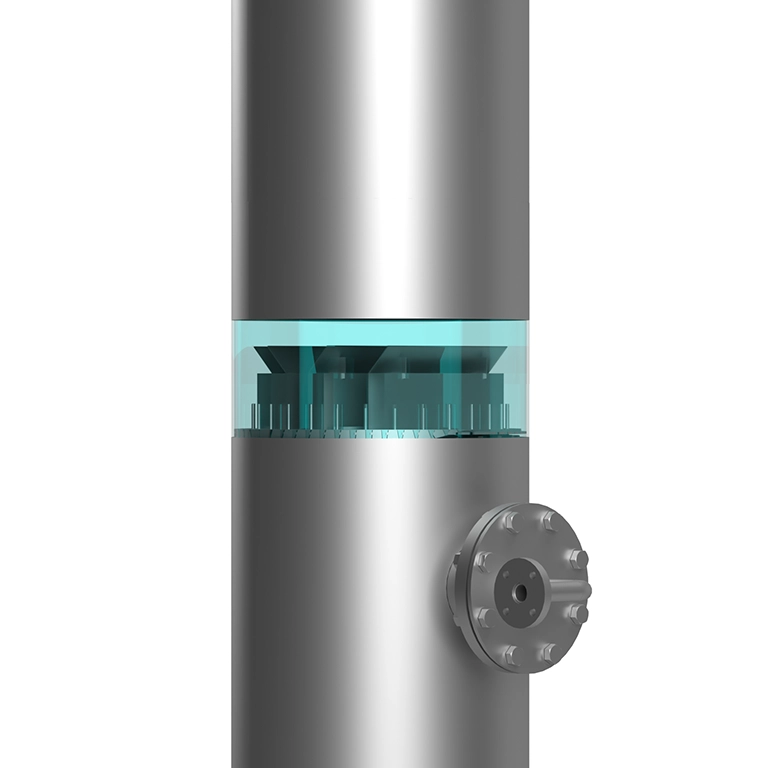
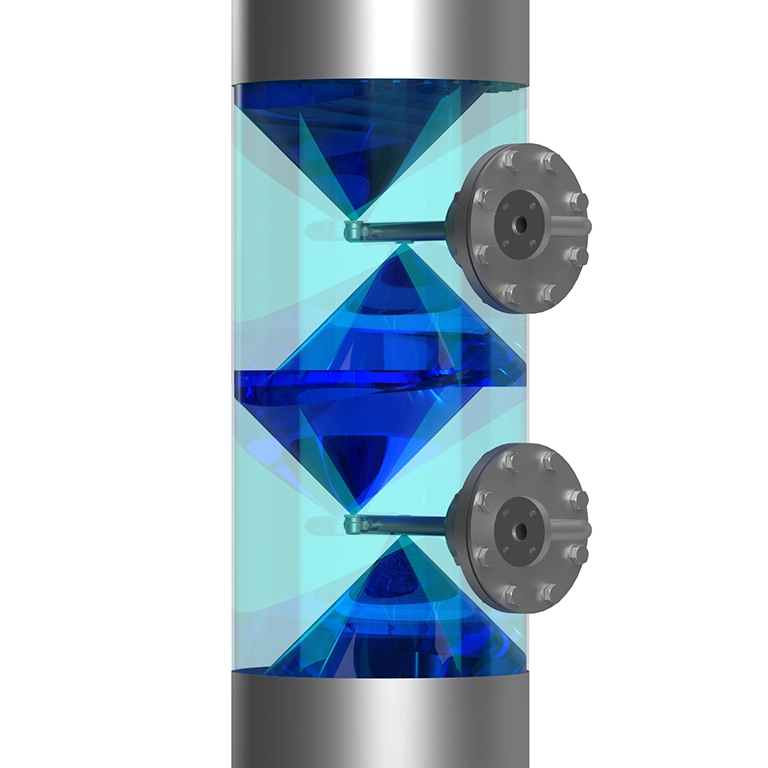
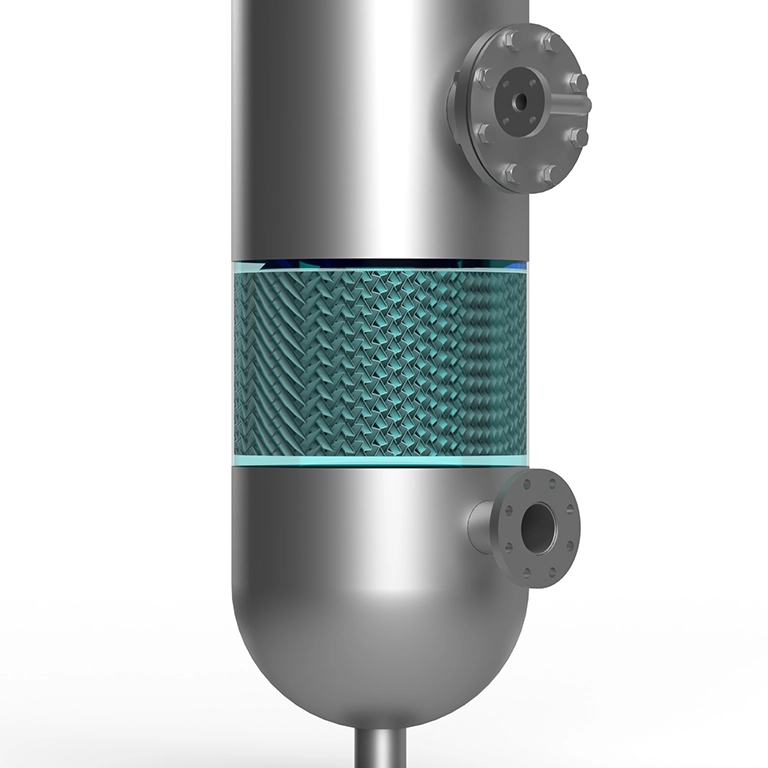
Packed bed scrubbers
Packings for absorption towers
In this type of scrubber a packing is used to create a large contact surface between gas and liquid to obtain a good absorption. Ceramics were initially utilized as the primary material for random packings in absorption towers. However, their susceptibility to damage, unfavorable volume-to-surface ratio, and high cost have led to a decline in their usage. As a result, the market is now predominantly dominated by metal and plastic packings. Metal packings are generally unsuitable for corrosive substances like acid gas, while plastic packings are not suitable for high temperature applications. Packed columns that follow a countercurrent principle are the most frequently used. When the waste gas moves upwards in the column, resistance is created due to the packings and the washing liquid flowing in the opposite direction. The pressure drop in the column depends on the gas and liquid flow rates, as well as the packings' specific surface area and free volume. A significant pressure drop requires a powerful fan to push the gas through the column, resulting in increased expenses. There are specific upper and lower limits for the washing liquid and gas flows in each column to ensure optimal performance. If the gas flow rate becomes too high, it can cause the resistance to the washing liquid to increase to a point where the liquid can no longer flow freely through the column. This leads to the accumulation of the washing liquid, blocking the entire gas surface and causing an increase in pressure drop. As a result, the washing liquid and gas are unable to mix effectively. When all the available space in the packings is filled with washing liquid and it starts to move upwards in the column, the scrubber is considered flooded. Most packed columns operate at around 60 to 70 percent of the gas flood rate, as operating a column under flooded conditions is not practical. Additionally, a minimum liquid flow rate is necessary to adequately irrigate the packings and facilitate efficient mass transfer between the gas and washing liquid.
Liquid distributor
A liquid distributor is specifically designed to ensure an even distribution of liquid throughout the packings and to facilitate a uniform contact between the liquid and gas phases. It is crucial for the liquid distributor to distribute the liquid evenly, prevent clogging and contamination, provide ample space for gas flow, and allow for operational flexibility. In taller columns, a liquid redistribution tray is often employed to collect liquid from the column walls and redistribute it towards the center of the column. This redistribution leads to improved contact in the lower section of the packings. Generally, fluid redistributors are required for every 2,500 to 6,000 mm of packing height, depending on the column diameter. There are two main types of fluid distributors: gravity-based distribution plates and pressure-based systems such as spray systems and perforated pipes. Nozzles are frequently used as distributor systems; however, they have the tendency to produce a fine mist that can be easily carried away by the gas stream. Additionally, they are prone to clogging and often necessitate high flows to compensate for inadequate distribution. On the other hand, liquid distributors typically comprise of flat trays with multiple gutters for gas flow and perforations in the tray floor for liquid flow. It is worth noting that the trays themselves can result in an undesired pressure loss in the gas flow.
Support plates
Support plates serve the purpose of providing a stable platform for packing materials to rest on. In fact, support plates can offer significantly larger open surface areas than the packings itself. This is achieved by effectively utilizing space in all three dimensions. Consequently, this feature can effectively alleviate concerns regarding pressure drop in processes with high flow rates. In addition, hold down plates play a crucial role in securing the packing materials in place.
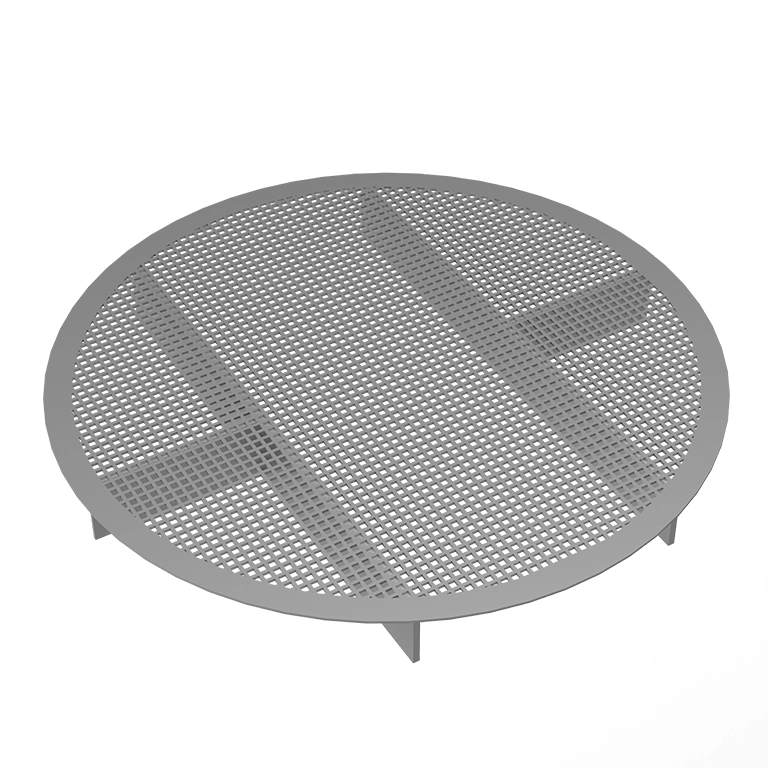
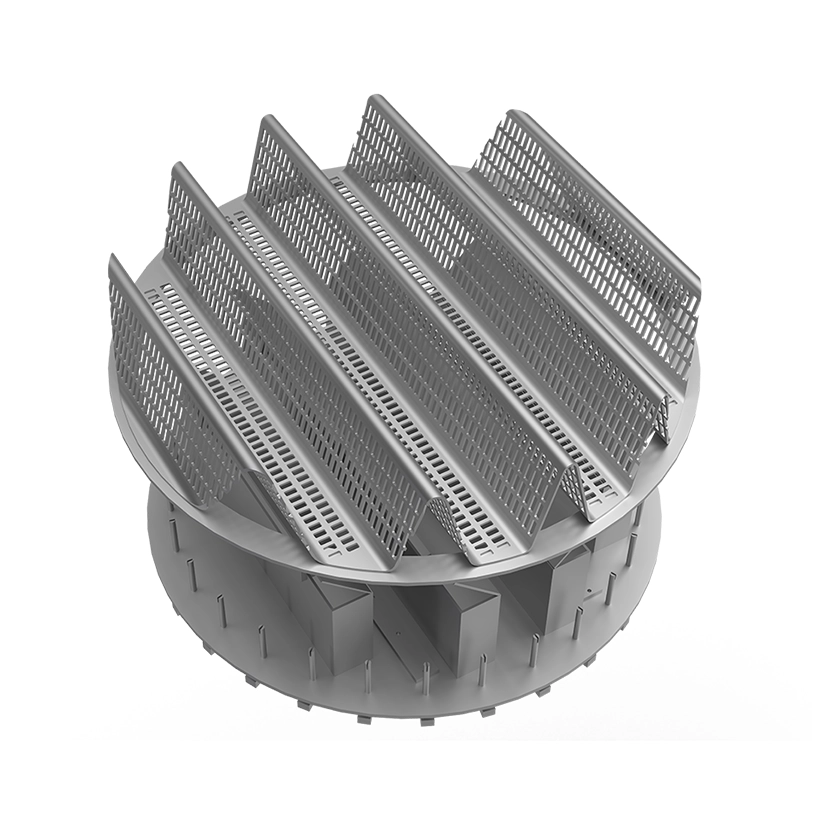
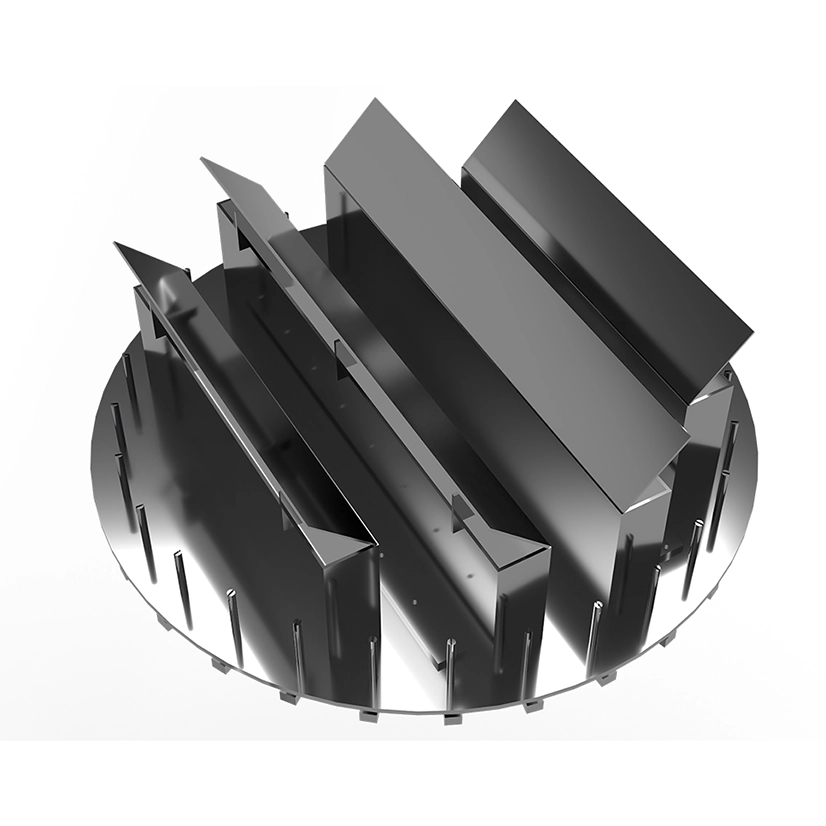
Hold down plates
On the other hand, hold down plates play a crucial role in securing the packing in its designated position. It is possible for random packings to be dragged along downstream processes of the column if a hold down plate is not mounted. While this is not a frequent phenomenon, it cannot be dismissed and has been witnessed in specific processes. Hold down plates keep the random packings contained within the column by providing their weight and resistance to the vertical force exerted by the gas phase. Bed limiters or hold down plates are devices used above the random packings to prevent fluidization, particularly during disrupted process conditions, and to restrict the movement of the packing. These limiters are designed to minimize interference with liquid flow.