High-Temperature Syngas Cleaning Scrubber System
The entire process of creating horizontal counter current scrubber installations involves designing, manufacturing, installing on site, and commissioning. These installations are specifically designed to effectively absorb pollutants and heavy tar components from a syngas flow that is generated within a biochar production system. The biochar itself is produced through the pyrolysis of biomass in an oven. After undergoing thorough cleaning in the scrubber, this syngas can be utilized as a viable alternative to natural gas.
The scrubber is comprised of interconnected and stacked modules. The foundation consists of flat stack containers that support various components such as liquid buffers, pumps, dosing systems, heat exchanger, electrical cabinet, clarifier, and drain tank. On top of the stackable flat rack, there is a flat rack bed where the separate washing sections and the fan are mounted. The modules are connected to each other on the gas side using flanges. The design of the installation allows for easy transportation of individual modules by truck or vessel, as well as convenient relocation on-site. As a result, the assembly time at the designated location is significantly reduced.
Principle horizontal scrubbers
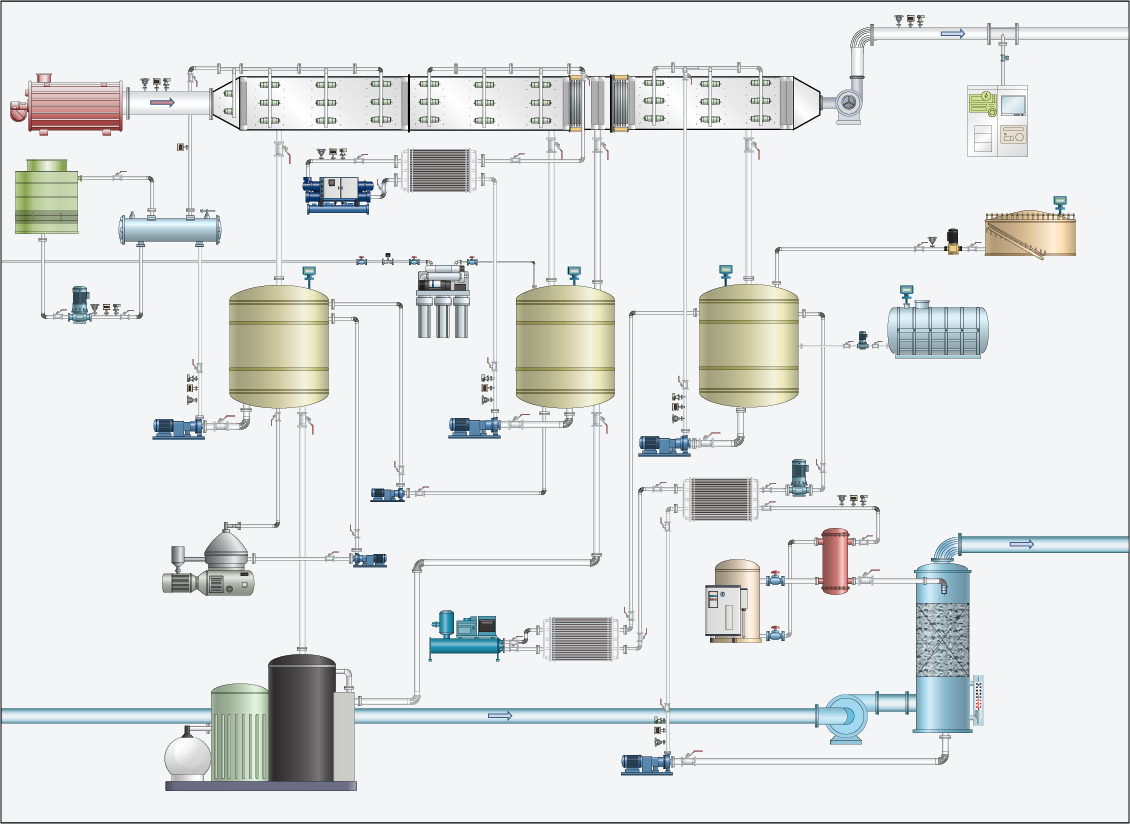
Open spray systems operate based on the difference in velocity potential between liquid droplets and the incoming gas. The liquid is pumped with moderate pressure through nozzles with the objective to achieve a homogeneous droplet distribution and a uniform spray pattern. The size of the droplets is of utmost significance as ultrafine droplets possess a significantly higher surface to volume ratio. The combination of these exceptionally fine droplets results in the formation of a fine mist, which effectively absorbs particles. These open spray scrubbers operate in a relatively straightforward manner and are characterized by their ease of maintenance and relatively low energy consumption.
Because there is no random or structural packing, the open spray scrubbers experience minimal pressure loss and are highly resistant to contamination. The scrubber operates using a closed-loop pump system, where the washing liquid is pumped from the buffer. By analyzing measurement values such as pH and conductivity, fresh water can be automatically added and drained based on the conductivity level detected.
The spray system is comprised of several detachable spray lances equipped with spray nozzles, some of which operate co-current while others operate counter current. The positioning of these spray nozzles within the scrubber is crucial in order to achieve optimal gas treatment by effectively capturing particles through intensive interaction between the washing fluid and the process gas. The tangential nozzles, which are designed to prevent clogging, generate fine droplets with a uniform spray pattern to maximize the absorption of dust and gas particles. Ensuring the finest liquid droplets come into contact with the gas and (dust) particles will result in a high level of absorption of pollutants.
The design of the spray section ensures the spray nozzles effectively clean the inside of the washing section by providing a high flow rate. The spray nozzles are strategically placed to create overlapping spray patterns, resulting in a intensive cleaning process. This system prevents the contaminated gas from passing through the spray section without being treated and cleaned. Consequently, there is no need for a packed bed, leading to minimal pressure loss that remains consistently low. This type of scrubber is particularly suitable for handling irregular concentrations, such as peak discharges, as it effectively utilizes the countercurrent washing principle.
Characteristics
- The counter current scrubber consists of a horizontal, rectangular housing made of AISI 316L which, seen in the flow direction, is made of multiple series-placed washing sections in which spraying is done with a combination of a caustic section with sodium hypochlorite, a neutral cooling section, and two non-polar solvent sections.
- The positioning of the spray nozzles in the scrubber is of the utmost importance for optimal gas cleaning for capturing particles through intensive absorption of the particles in the process gas. Optimal contact of fine liquid droplets with gas and dust particles will lead to a large uptake of polluting components.
- The scrubber is constructed, seen in the flow direction, of four series-placed washing sections which are structurally identical. Each washing section is equipped with multiple spray arms in a row on which essentially clogging-free nozzles are mounted to obtain a long spraying path. The spray arms are mounted in such a way that the nozzles rinse the inside of the washing section well at the same time.
- Each washing section is equipped with an inspection hatch so that the rectifiers, spraying nozzles, and droplet separators can be checked and possibly cleaned very easily.
Section 1: Pre-washing and Quenching
Because the syngas has a high inlet temperature (>500°C), it is imperative to rapidly cool the gas to mitigate the risk of explosion. Consequently, the pre-washing section also functions as a quenching process. The washing liquid is cooled below the solidification point of the heavy TAR components in order to solidify them. This enables the removal of the solids using a clarifier, allowing for the reuse of the washing liquid. To prevent any pollution of the rectifier's vane profiles, spray nozzles are used in the pre-cleaning section. These spray nozzles ensure that the entire surface at the front is covered with spraying liquid, effectively preventing any entrained particles from causing clogging. In the case of relatively dry gas, rapid evaporation occurs, resulting in adiabatic cooling. Consequently, the gas temperature decreases to the wet bulb temperature. The extent of temperature drop depends on the moisture content of the incoming gas. For saturated gas, a heat exchanger is utilized to cool the washing liquid using external cooling water.
- The rectifier is utilized to laminate the gas flow due to the inability to clean the incoming turbulent airflow. It consists of cassettes that contain vane profiles, allowing for convenient removal of the rectifiers for inspection and cleaning purposes.
- The gas flow is purified by a vane type separator section, which effectively removes the droplets. This droplet separator consists of cassettes that can be conveniently disassembled for inspection purposes. These cassettes are placed in a guidance gutter within the scrubber. The compact design of the cassettes allows for easy removal through an access hatch. In case the separator profiles require cleaning, it can be effortlessly accomplished by detaching the cassettes and utilizing a high-pressure cleaner
Section 2: Alkaline oxidation section
- The alkaline washing section utilizes a caustic soda solution to absorb and neutralize the acid-forming elements. The chemicals are carefully measured and added to the buffer tank, while the pH level and conductivity of the washing water are constantly monitored. This ensures that the precise amount of caustic soda is automatically dosed.
- This section operates at even lower temperatures to achieve further solidification of components. In case of excessive conductivity, the washing fluid is drained back to the first section where the solid components can be removed with the clarifier.
- To prevent water droplets from contaminating the biodiesel with glycerol, a highly efficient double acting vane type separator is deployed. This droplet separator effectively removes any entrained water droplets, maintaining the purity of the biodiesel.
Section 3: Biodiesel-glycerol purification stage
- In the third stage, the purification process involves using a washing liquid consisting of biodiesel and glycerol. This stage is crucial for effectively absorbing the lighter TAR components. The absorption liquid utilized is a combination of biodiesel and glycerol. The supply and drainage of biodiesel and glycerol will be regulated based on the readings from the FT-IR analyzer, which is installed in the exhaust system.
- A double vane type separator is deployed to remove entrained droplets. This vane separator is also constructed with cassettes that can be easily disassembled for inspection and cleaning. Compared to the intermediate separators used in the other washing sections, this vane separator system offers a higher efficiency.
Stripper
The liquid stripping column is deployed to eliminate the substances that have been absorbed by the biodiesel section from the third stage of the horizontal scrubber. This stripping column is constructed with a vertical stainless-steel structure and utilizes random packings for distribution, facilitated by spray nozzles. The countercurrent principle serves as the foundation for the stripping tower, while the pressure difference is closely monitored to regulate the pressure drop of the packings and the wire mesh demister.
Heat exchangers
Heat exchangers have been selected for the cooling processes required in the system to ensure the proper operation of both the scrubber and the stripper. In the case of the scrubber, heat exchangers are utilized to cool the washing liquid and quench the syngas by passing it through chilled water.
As for the stripper column, the heat exchangers serve as heaters for the biodiesel. The third section and the stripper in the system are designed and incorporated in a way that maximizes the utilization of the existing energy by heating and cooling the liquid flows. The stripper can be externally heated using steam, for instance. The discharge return flow from the stripper is utilized to preheat the incoming liquid flow to the stripper to save a huge amount of energy.